
Headquarters Renovation
An European manufacturer recognized it needed to reinvest in their North American headquarters to increase productivity and reduce costly employee turnover. The project began as a simple refresh but expanded into a total overhaul of the office portions of the campus.
The project included a deep dive into understanding the company, the way its employees and their teams function, and their needs, both met and unmet. We partnered with a GC to provide continuous feedback on constructability and price.
My role was lead project architect and designer, working with a two interior designers and a project manager.
— Plymouth, MN
— 45,000 SF
— GMP Delivered February 2020
Campus Aerial. Project area highlighted in blue (1 & 2). 3: Food Application Center- a place to take clients to oversee ongoing projects. 4: Production facility, 5: Warehouse.
Above and below show the scope of work and existing conditions. The office is an unintentional product of years of quick fixes. The office portion was originally a single-floor industrial facility. In the mid-’90s, during a contraction, the company vacated their main office building and transformed an underused portion into their office with the addition of a second level inside the building shell. This created a dark, cavernous floor plate with little natural light.
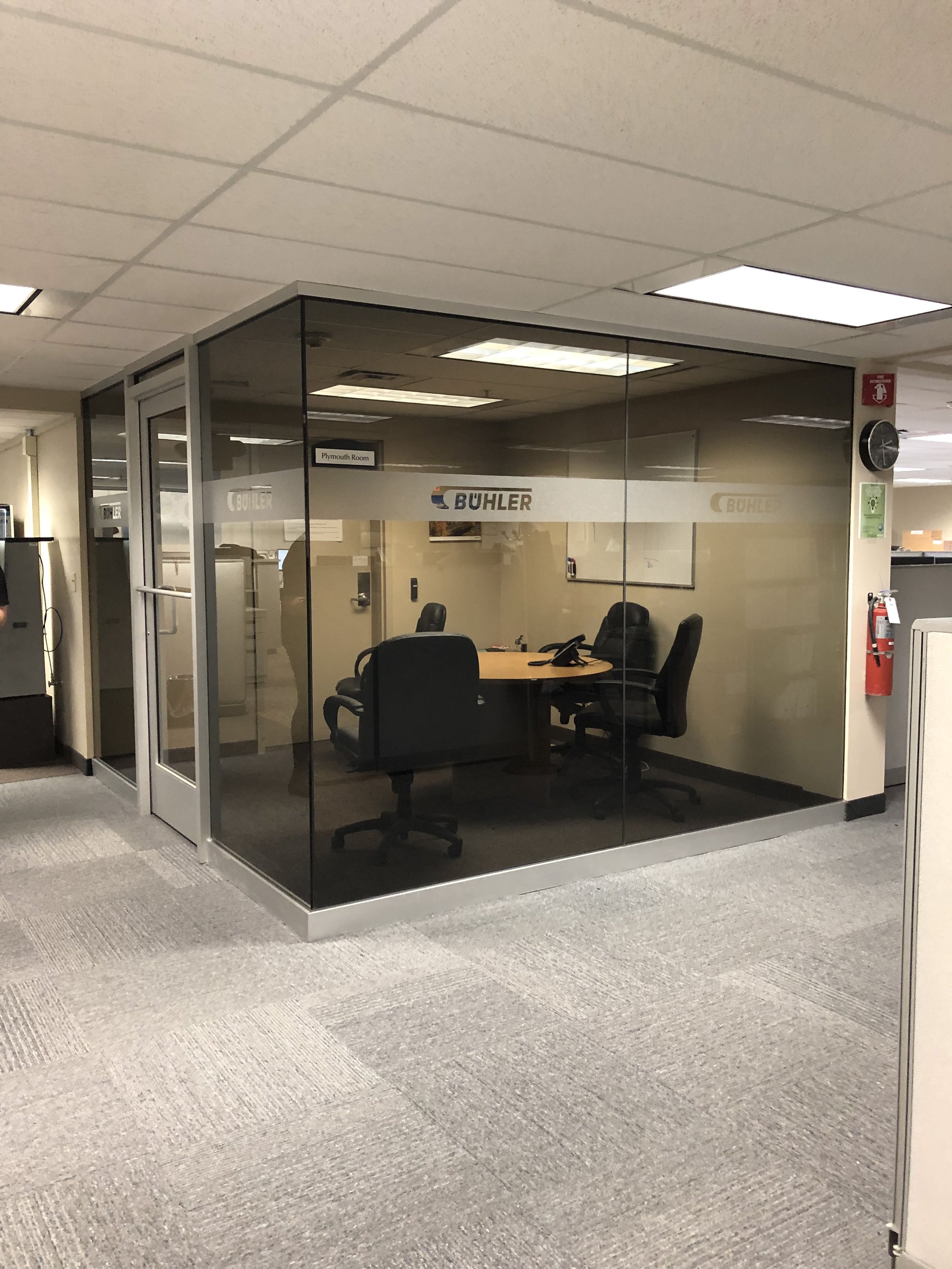
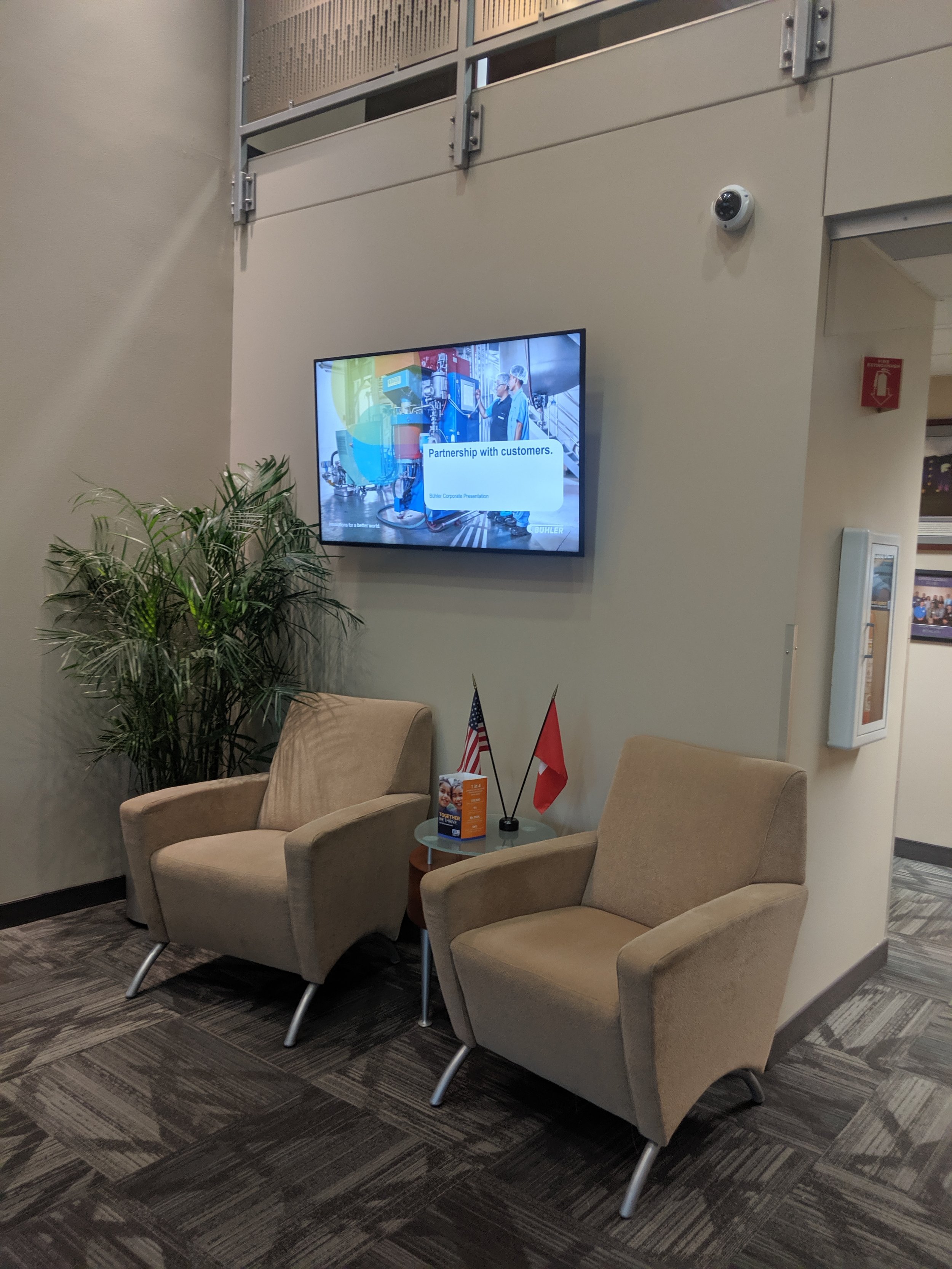
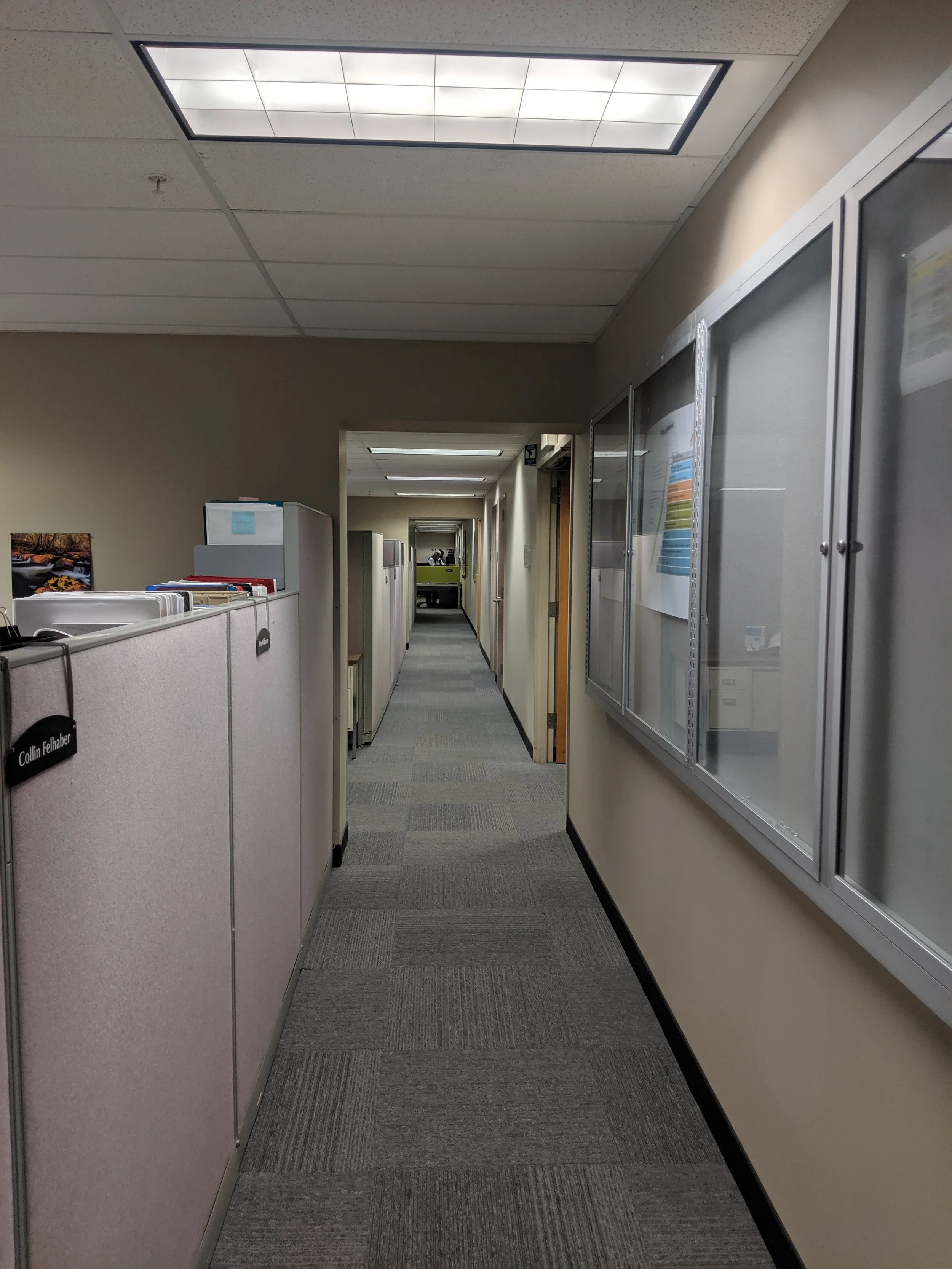


Programming Exercise
-
Engagement
The first step was on-site user engagement with key members representing teams across the entire company. Needs, wishes, complaints, and ideas were all discussed openly.
-
Survey
Using knowledge from the on-site engagement session as well as office walkthroughs, we conducted a focused survey addressing key concerns. We used this to gain an understanding of company structure, team-specific needs, and intra-team collaboration.
-
Existing Analysis
A separate, simultaneous process with facilities, consultants, and the contractor helped us understand the technical limitations and needs of the 50-year old building.
Interviews, the survey, and daytime observation allowed us to create an adjacency diagram to maximize plan efficiency and make most of the limited space.
Level 1 of the new plan. This plan features clear sightlines, a hierarchy of organization, and an equalized access to light and amenities.
Level 2 of the new plan.
Entry Experience
New, expanded entry
windows to allow light transfer deeper into the work areas
New boardroom in a prominent location
Client-facing coffee lounge/reception
Clear sightlines to interior offfice
New entry stair
Direct sightline and new windows into “Machinery Showroom”
Light Well
Stair (previously enclosed) opened to encourage more walking and allow better light transfer.
New catwalks created by selectively removing parts of level 2.
New skylights to allow light penetration in what had been the darkest space in the office.
New outdoor amenity area.
Microwaves/refrigerator area kept away from main kitchenette. This keeps messes and smells away from the work cafe.
The work cafe, a new gathering space for teams or individuals.
Conference rooms abut the space, mitigating sound transfer. Each room has glazing for daylighting.
New reception view from entry. Boardroom above client coffee lounge. Direct view to machinery showroom.
View from showroom back towards entry, showing new stair.
View at light well, showing new skylights and new floor openings.
View at renovated cafe.
New entry and signage at exterior visitor parking.
Typical work area, with equalized access to light, more connections between levels, and more collaboration spaces.